Advantages of injection molding
Injection molding is characterized by high dimensional accuracy. The injection process allows for the production of high-quality parts without the need for secondary finishing and allows for much shorter production cycle times than other processes. The disadvantages are the higher cost of molds and machines, although they can be compensated for by higher productivity.
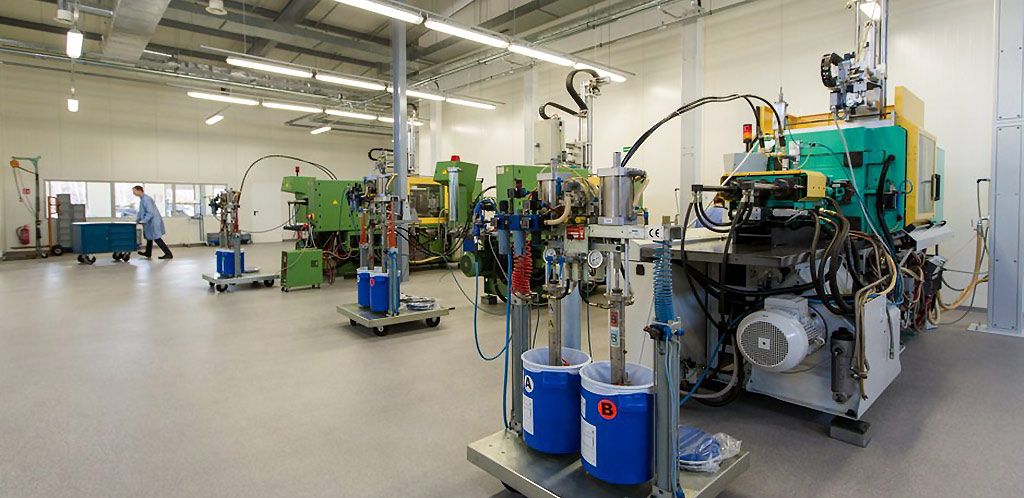
Injection molding is especially recommended for high volume production of small to medium sized components such as:
- Teats for baby bottles
- Sealing rings
- Suction cups for the automation of production processes
- Medical components
Material selection
Both solid silicone and liquid silicone are suitable materials for injection molding.

Injection molding process
Dosing and mixing
Liquid silicone rubber is supplied in two-component form, in 2 x 20 kg containers or in 2 x 200 kg drums. The dosing unit pumps components A and B directly from the containers or drums in a 1: 1 ratio into the mixer and further into the injection cylinder of the injection molding machine. If necessary, the dye is supplied to the mixer via a separate line.
HCR
Solid silicone can be supplied:
- ready for processing in the form of blocks, strips, ribbons, etc.
- in the form of a base ingredient to which crosslinkers and other additives need to be added. The addition takes place on a rolling mill.
The solid silicone is fed into the injection cylinder of the injection molding machine either directly for ribbons and strips or via a special cylinder with a piston.
Injection and vulcanization
LSR – There are two ways to bring the material to the seat: direct fill, cold runner and indirect fill (cold nozzle and hot sleeve). Each method has its own advantages and disadvantages.

Direct infusion
The material is injected into the cavity through a cold channel. The cold runner needle valve system has additional advantages such as less shear on injection.
Advantages:
- the products do not require additional processing (no ingot and flashes)
- possible high degree of automation
- less material consumption (no ingot)
Defects:
- high cost of designing and manufacturing an injection mold
- higher costs of a multi-cavity injection mold (requires a separate cold runner for each mold)
Indirect infusion
Material is injected into the seat through an injection sleeve and gating channels. The vulcanized ingot must be removed into the mold with the product.
Advantages:
- cheaper mold making
- Suitable for low and medium batch sizes
Defects:
- higher material consumption (ingot waste)
- additional processing required (removal of the ingot and flashes)
- unsuitable for fast-crosslinking systems (risk of scorching in runners)
Cross-linking temperatures and times depend on the quality of the heating system and the material, size and shape of the manufactured detail. Most often, liquid silicone is processed at a temperature between 150 ° C and 200 ° C.
HCR
Solid silicone offers similar advantages to LSR. However, due to the majority of the material viscosity, the ingot cross-sections are larger.
Solid silicone is processed at temperatures between 150 and 200 ° C.
Removal of moldings
Vulcanized silicone tends to stick to the mold walls. There are several ways to solve this problem.
Multiple cycle passes
Removal of moldings can be difficult at the beginning of the process. After many cycles, a silicone-based anti-adhesive layer builds up on the mold, which facilitates the removal of the moldings.
Release agents
The use of special release agents supports the separation of the molded parts from the mold at the beginning of the process.
Optional accessories
Details can be removed by the use of ejectors and brushes or blower units.
